Improving packing line efficiency
Researchers based at the STFC Hartree Centre are working with Unilever to optimise their packing line operations using the power of data.
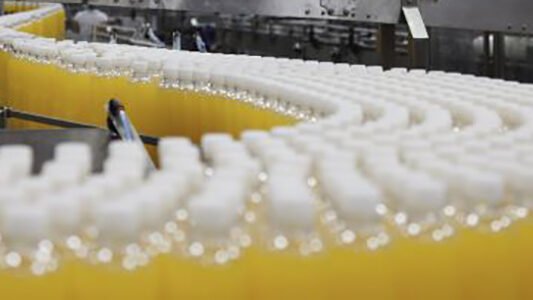
Challenge
Automated packing lines for Fast-Moving Consumer Goods (FMCG) – including toiletries, packaged food, and over-the-counter pharmaceuticals – process hundreds of product units per minute and run close to 24 hours a day, 7 days a week. Packing lines inefficiencies occur due to unplanned stoppages, for example due to mechanical or electrical faults, or minor problems which need to be rectified by an operator. The high throughput of the lines means that relatively small changes in stoppage rates can equate to a difference of millions of units processed per year. Unilever wanted to understand and optimise their packing line operations by making use of the large volumes of data automatically collected from the lines.
Approach
The research team used big data workflows on the Hartree Centre’s high performance computing systems to align millions of packing line machine error messages with line rate data at a resolution of one second or more, providing a full picture of the operation of each line. The team then used data science techniques to derive insights as to where, and to what extent, efficiency improvements could be made – for example, analysing the overall impact of certain types of machine errors or product changeovers online productivity.
Benefits
Completed as part of the Innovation Return on Research (IROR) programme, a collaboration between STFC and IBM Research, the analytics from the project showed in detail the opportunities for improvement to Unilever’s packing lines, enabling them to target line performance improvements much more efficiently. The tools developed during the project can now be applied to derive analytics from any manufacturing data in FMCG and other sectors, accelerating data-informed decision-making to improve production operations.
“This very thorough analysis with clear visualisations of these complex data sets has revealed new insights that have helped us prioritise the key areas for focus in order to improve the efficiency of our manufacturing process.”
Adam Kowalski, Unilever
Join Newsletter
Provide your details to receive regular updates from the STFC Hartree Centre.