Bringing supercomputing to the factory floor
The Hartree Centre has provided critical assistance to simulation company 3DSIM to optimise its software, which reduces the risk of failure during metal 3D printing.
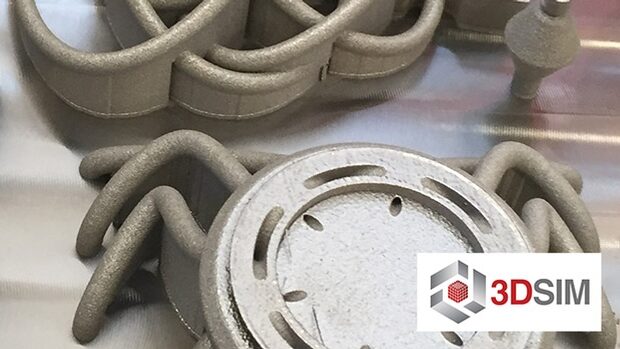
Challenge
3D printing is fast becoming a choice that many manufacturing companies turn to for the design and production of complex shapes or parts in challenging materials. Also known as additive manufacturing (AM), the technology is simple in principle; the desired component is created through the assembly of many thousands of slices or layers, with the addition of each slice eventually resulting in an completed part. In practice, however, the process is complex, particularly for metals where the market value is estimated in the region of $3Bn in 2015-16 and shows no sign of decreasing. One principle barrier prohibiting the uptake of AM technology is a lack of versatile and accurate simulation tools which model how a part will build, and predict potential failures. Such failures waste materials and production time, and can damage the AM platform (worth $500,000+ per machine). 3DSIM have created a software to predict and prevent these losses, but this kind of simulation is incredibly computationally intense and therefore usually time-consuming to run, even on a supercomputer.
Approach
3DSIM accessed the Hartree Centre’s software development expertise to optimise its AM simulation software run quickly and efficiently on both CPU and GPU platforms. This was critical in enhancing the performance of the core code and enabling it to run in minutes rather than years, a significant competitive advantage over many alternatives.
Benefits
The overall processing time was significantly reduced whilst increasingly the overall fidelity of the simulation, reducing the simulation compute time from decades down to minutes. This was a pivotal requirement for the company to build a commercially viable platform. 3DSIM’s simulation technology is designed to resolve the problem of potential AM failures by accurately predicting distortion during build, and consequently adding or subtracting material to allow a successful construction first time. Thanks to the Hartree Centre’s assistance in optimising the software, it can now be run on GPU based systems, allowing effective deployment through cloud computing. This means that, irrespective of the size of the company, full simulation capabilities can be utilised, making AM technology more accessible to a more diverse range of manufacturing companies – including SMEs that might have previously found the possibility of expensive build failures too risky. This improves such companies’ ability to maintain their stake in a fast-moving and competitive industry, while also enabling them to enhance their product range.
Join Newsletter
Provide your details to receive regular updates from the STFC Hartree Centre.