Improving Electric Vehicle Batteries through Immersion Cooling Simulations
STFC Hartree Centre worked with Faraday Battery to explore the potential of immersion cooling to enhance electric vehicle battery efficiency through the Innovate UK A4I programme.
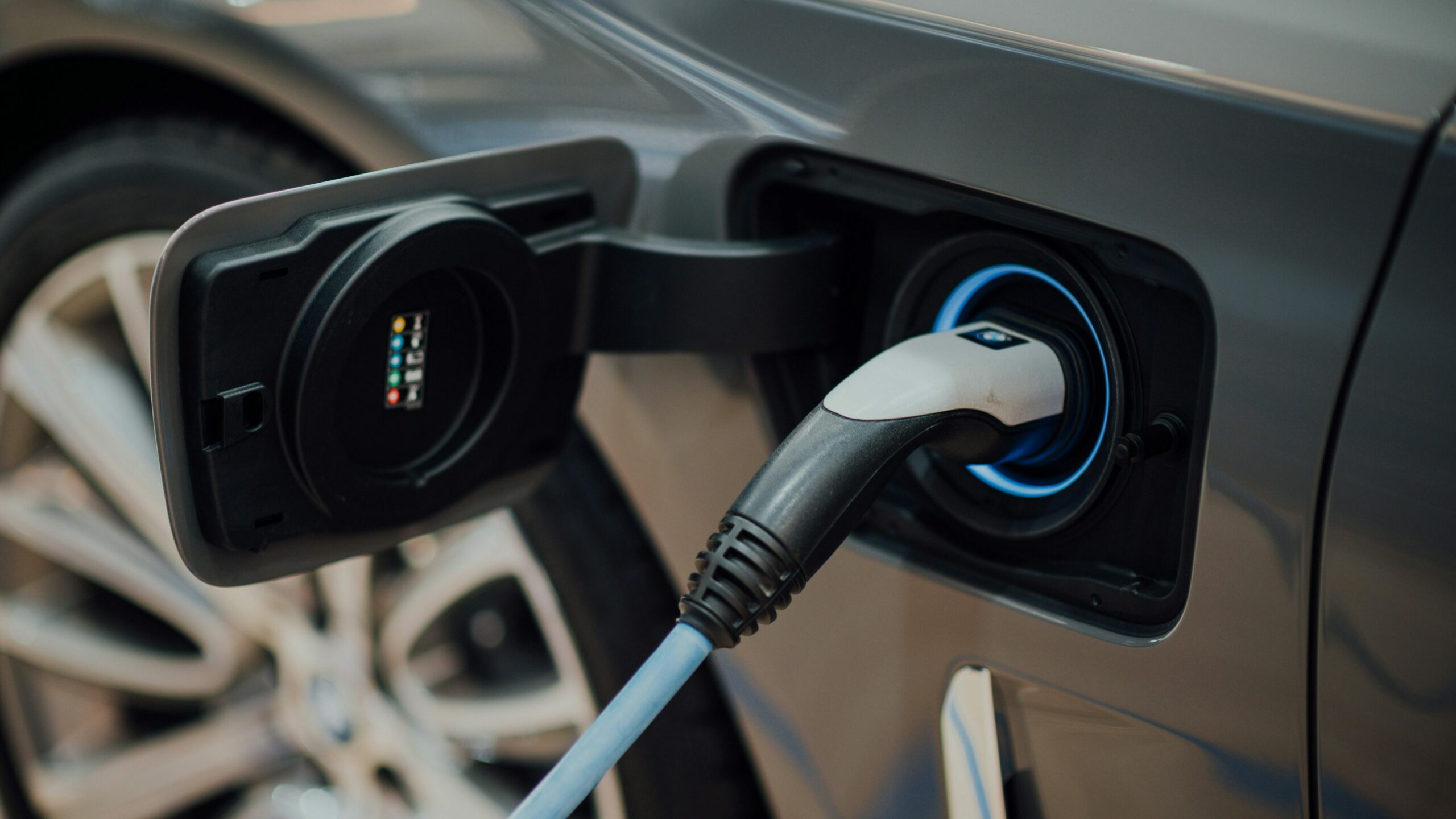
Challenge
As governments are looking to create a greener future, the demand for battery Electric Vehicles (EVs) is surging. However, meeting this demand comes with major challenges, like the cooling of EV batteries which can produce a lot of excess heat. Conventional air and liquid-cooling methods often fail to provide uniform battery temperature which can cause overheating leading to hotspots, reduced efficiency and shorter battery lifespans. Faraday Battery is working to help resolve these challenges and improve consumer adoption of EVs by looking at Immersion cooling, a closed system of coolant in the battery surrounding the cells.
Approach
Our high performance computing experts used OpenFOAM, a simulation software, to help Faraday Battery run simulations and model how the coolant works when coming into contact with the battery cell. They also created a report to explain the functionality of the software, describing the physics considerations and assumptions. The high performance software engineers also did a practical usage of the simulation by testing the battery cells being emerged in different depths of coolant. Even with low amount of coolant it showed the cooling rate would be efficient. We also helped Faraday Battery to install OpenFOAM and showed how to adjust it for future experiments.
Benefits
To help build a greener future, we need more efficient batteries for electric vehicles, and we worked with Faraday Battery to optimise their battery design process. EVs require efficient batteries which last longer, charge faster and can drive further distances. However, real-world tests of multiple variables are expensive and time-consuming. Our experts helped Faraday Battery by inputting the data from one test into their model so that they could trust that the simulation was accurate and test for multiple other variables like the starting temperature of the coolant. This helped the company grow their autonomy to be self-sufficient, speeding up the battery design process to create a re-circulating battery coolant.
“STFC stands as a beacon of unparalleled expertise, offering a depth of capability that far exceeds what any small SME team might achieve. Gaining access to STFC is not merely an opportunity—it is a privilege, for their collaborative spirit and excellence make them an extraordinary team to work with.”
Sanjay Gupta, Faraday Battery
Join Newsletter
Provide your details to receive regular updates from the STFC Hartree Centre.